Galvanized Steel: Types, Uses, Benefits.
Part of an ongoing series on Galvanized Steel
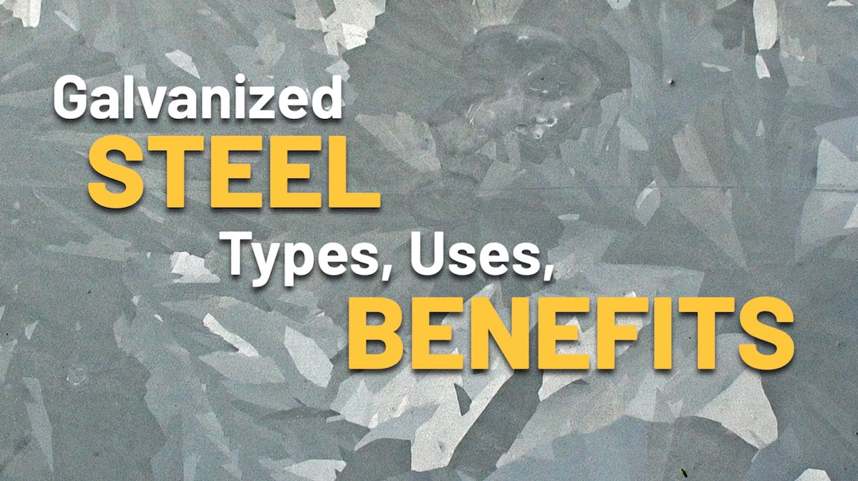
What is Galvanizing?
Galvanizing, or galvanization, is a manufacturing process where a coating of zinc is applied to steel or iron to offer protection and prevent rusting. There are several galvanizing processes available, but the most commonly offered and used method is called hot-dip galvanizing.
Galvanized steel is among the most popular steel types because of its extended durability, having the strength and formability of steel plus the corrosion protection of the zinc-iron coating. The zinc protects the base metal by acting as a barrier to corrosive elements, and the sacrificial nature of the coating results in a long-lasting and high-quality steel product.
This versatility makes it applicable to a variety of projects and industries, including agriculture, solar, automotive, construction, and so on. Below, we aim to provide a comprehensive description of how galvanized steel is processed, different galvanization methods, its benefits, and how it is used in these various industries.
Get a Custom Quote for Your Galvanized Steel NeedsThe steps in the galvanizing process are as follows:
- The steel is cleaned in a degreasing solution
- After being cleaned, the steel is pickled by being lowered into a vat of diluted hot sulfuric acid
- The steel is then fluxed in an aqueous solution (typically zinc-ammonium chloride)
- After the flux, the steel is galvanized through immersion in a vat of molten zinc
- Afterward, the steel is inspected for consistency and a complete coating
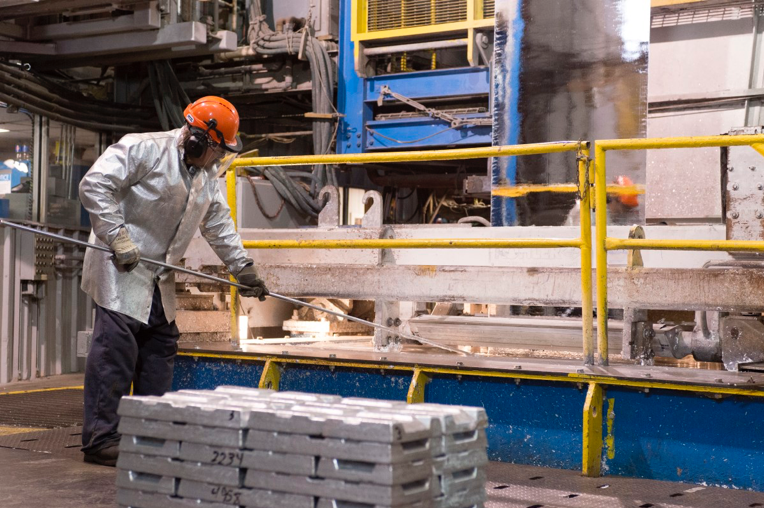
What are the advantages of galvanized steel?
Many different industries utilize galvanized steel primarily because it has such a wide array of benefits for industries to take advantage of, including having:
Low initial cost compared to most treated steels. In addition, galvanized steel is immediately ready to use when delivered. It does not require additional preparation of the surface, inspections, painting/coatings, etc. sparing companies more costs on their end.
Longer life. With galvanization, a piece of industrial steel is expected to last more than 50 years in average environments, and can last over 20 years with severe water exposure. There is no maintenance required. The increased durability of the steel’s finished product also increases the product’s reliability.
The sacrificial anode ensures that any damaged steel is protected by the surrounding zinc coating. It doesn’t matter if the steel section is completely exposed; the zinc will still corrode first. The coating will corrode […]