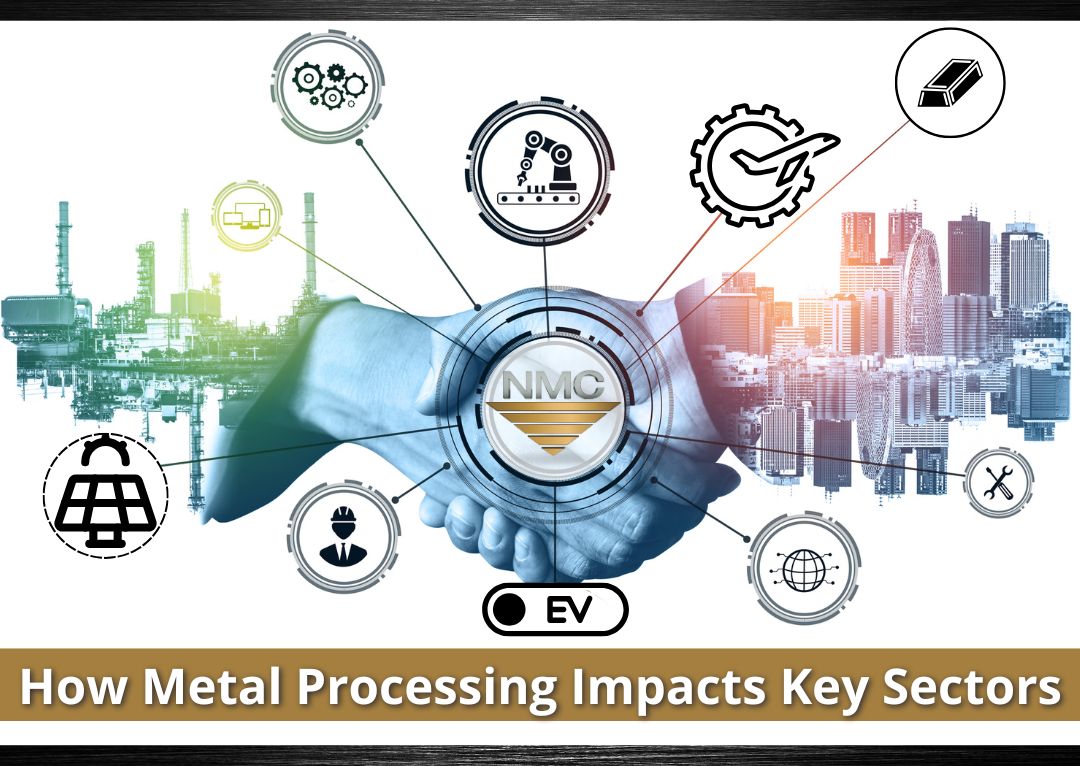
Main Takeaways
- Metal processing impacts key sectors such as aerospace, automotive, construction, and renewable energy, driving innovation and efficiency.
- Lightweight metals like aluminum alloys and AHSS enhance fuel efficiency, structural integrity, and performance in industries like EV production and aerospace engineering.
- Precision steel slitting, galvanized steel processing, and aluminum extrusion are crucial for manufacturing durable, high-performance components across multiple sectors.
- National Material Company (NMC) provides tailored metal processing solutions, leveraging cutting-edge expertise, supply chain efficiency, and sustainability initiatives. Partnering with NMC ensures access to industry-leading capabilities in steel processing, aluminum extrusion, and supply chain management to support your next project.
For engineers, procurement specialists, and industry leaders, selecting the right materials isn’t just about meeting specifications, it’s about driving innovation and solving real-world challenges. Whether you’re designing fuel-efficient aircraft, lightweight electric vehicles, durable infrastructure, or sustainable solar energy systems, one thing remains clear: metal processing impacts key sectors in profound ways.
From advanced high-strength steels (AHSS) to aluminum extrusion, modern metal processing techniques are shaping the future of aerospace, automotive, construction, and renewable energy. This article explores practical applications, industry advancements, and emerging trends like green steel production, providing insight into how these innovations can drive efficiency and sustainability.
Lightweight Metals for Soaring Innovations
The aerospace industry relies on lightweight yet durable materials to optimize performance and efficiency. Aluminum alloys, titanium, and specialized steels are essential for reducing aircraft weight while maintaining structural integrity and safety. As metal processing impacts key sectors like aerospace, advancements in material science and manufacturing techniques continue to push the boundaries of innovation.
For example, aluminum extrusion techniques allow manufacturers to create complex shapes that optimize aerodynamics and fuel efficiency. According to Taber Extrusions, alloys in aerospace applications can withstand extreme temperatures and pressures, ensuring safety at 35,000 feet.
One fascinating insight is the growing use of additive manufacturing (3D printing) in aerospace metal processing. By layering metals like titanium and stainless steel, engineers can produce intricate components faster and with less waste than traditional methods. This shift also supports sustainability initiatives, demonstrating how metal processing impacts key sectors by minimizing material consumption while enhancing precision and performance.
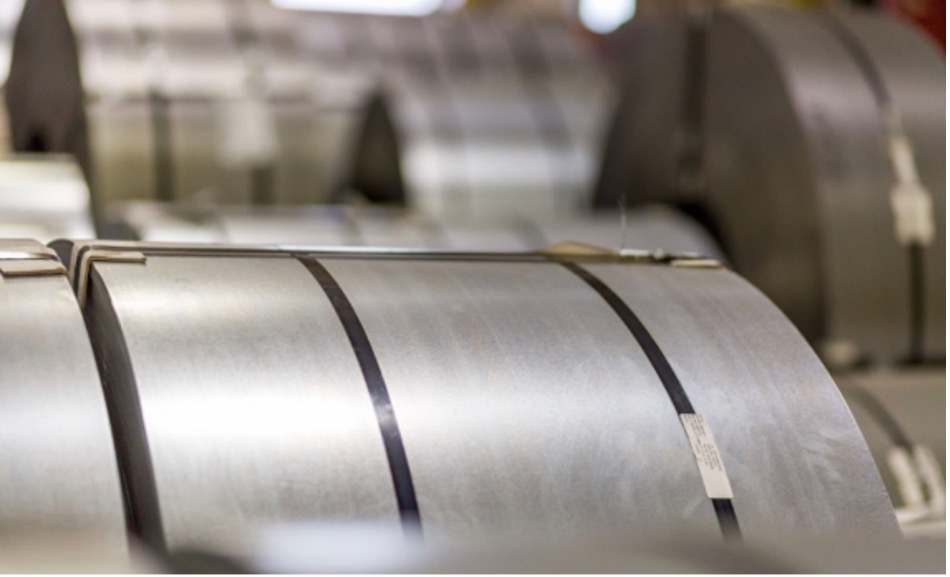
Galvanized steel also finds its place in aerospace infrastructure, such as hangars and maintenance facilities. Its corrosion-resistant properties ensure longevity even in harsh environments. These innovations underscore how metal processing impacts key sectors by enabling safer, more efficient air travel.
Paving the Way for Electric Vehicles
As the automotive industry accelerates its shift toward electric vehicles (EVs), the need for advanced metal processing is more critical than ever. Metal processing impacts key sectors like automotive manufacturing by ensuring the production of strong yet lightweight materials essential for EV design and performance.
Steel processing remains essential for producing robust frames, while aluminum processing provides lightweight alternatives for battery enclosures and body panels. Advanced high-strength steel (AHSS) is particularly noteworthy — it delivers exceptional crash resistance without adding excessive weight, a key factor in optimizing EV range and efficiency.
Tesla’s Model 3
Take Tesla’s Model 3, for instance. Its chassis incorporates AHSS and aluminum alloys to balance strength and weight. Similarly, Ford’s F-150 Lightning uses military-grade alloy bodies to enhance performance and durability.
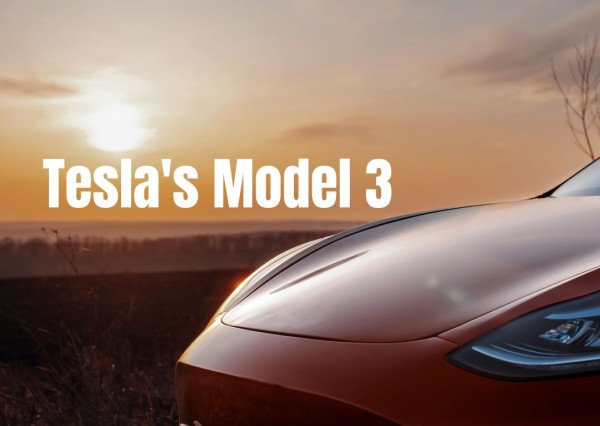
Behind these innovations lies a sophisticated supply chain management system that ensures timely delivery of processed metals to assembly lines. Steel slitting plays a crucial role in EV production as well. Precision-cut galvanized steel coils are used in EV motor housings and electrical systems, ensuring long-term reliability under demanding conditions. With global EV sales projected to surge, the demand for sustainable and efficient metal processing solutions will only continue to rise.
Building Stronger, Smarter Structures
Metal processing impacts key sectors in construction by providing materials that meet stringent safety and sustainability standards. Galvanized steel beams, for example, resist rust and corrosion, making them ideal for bridges, skyscrapers, and residential buildings. Meanwhile, aluminum extrusions offer flexibility in designing modular structures, which are increasingly popular in urban development.
Emerging trends, such as circular economy practices, influence construction material choices. Recycled steel and aluminum are being integrated into new projects, reducing environmental impact. Digital tools powered by AI and machine learning (ML) further enhance quality control during fabrication, ensuring consistent performance across large-scale projects.
Consider Dubai’s Burj Khalifa — the tallest building in the world. Its foundation relies heavily on reinforced steel, while its façade features aluminum cladding for thermal efficiency. Such examples highlight how metal processing drives architectural innovation worldwide.
Powering a Sustainable Future
Metal processing impacts key sectors like renewable energy, where durable, high-performance materials are essential for both functionality and longevity. Solar energy systems depend on reliable metals to withstand harsh environmental conditions over decades of operation. Aluminum frames support photovoltaic panels, offering corrosion resistance and UV durability, while galvanized steel is commonly used in mounting structures to provide stability against wind and seismic forces.
Wind turbines present another compelling case. Their towers require thick steel plates capable of bearing immense loads, while rotor blades incorporate lightweight composites reinforced with aluminum alloys. These materials must endure constant mechanical stress, making rigorous quality control in metal processing essential for long-term performance and reliability.
The renewable energy sector is also driving demand for green steel production. Technologies like hydrogen-based direct reduction and electric arc furnaces significantly reduce carbon emissions, aligning with global decarbonization efforts.
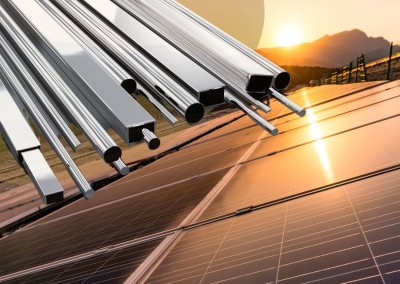
By adopting sustainable metal processing techniques, manufacturers not only support the shift toward clean energy but also meet the growing demand for renewable infrastructure.
Why National Material Company Stands Out
In tackling the challenges encountered by these sectors, NMC and its affiliated companies thrive by leveraging collaboration and expertise. They specialize in everything from steel slitting to extrusion, delivering tailored solutions that meet diverse needs. Their commitment to sustainability and digital transformation ensures they stay ahead of industry trends.
For instance, Gibbs Interwire, part of the NMC family, supplies custom wire products for aerospace and automotive clients. Meanwhile, Taber Extrusions provides precision aluminum extrusions that are critical for renewable energy projects. Together, they form a robust network capable of handling complex supply chain requirements.