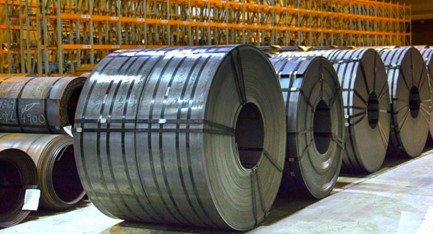
There are many steps required in metal processing in order to achieve a high-quality product. American steel processor, National Material Company (NMC), believes there can be no exception to this rule. Steel is an alloy that is a mixture of both iron and carbon and it is durable, sustainable, and highly desired by many industries. Formal specifications and different grades of steel can affect the performance and use of the metal, but there are additional techniques within the metals’ processing that can alter the strength and finish. In this article, we will focus on one technique known as cold rolling.
Engineers and designers alike must decide on the type of metal they will need to begin work on their projects. Cold rolled steel for many reasons might be the ideal metal. “Cold rolled” refers to the process the steel undergoes before becoming the final product. The temperature is not what we may consider “cold.” Instead, the entire process occurs at room temperature and involves applying great pressure to the steel. However, this does not mean cold rolled steel never experiences its recrystallization temperature. In fact, cold rolled steel endures extreme temperatures and compression rollers just like hot rolled steel. Cold rolled steel simply undergoes more processes once it has cooled down to get exact dimensions and better surface qualities. In many cases, steel may undergo processes like rolling, turning, grinding, and polishing. Each one gives the steel a unique finish.
There are many advantages of cold rolled steel, such as increased strength. (Read about Advanced High Strength Steel, or “AHSS” here.) The compression of the steel at room temperature hardens the strain, giving the metal significant strength when compared to other types of steel. That being said, the steel is not needlessly thick to create this strength. Cold rolling allows for tighter tolerances not found within other steel manufacturing. In other words, the metal will have thinner walls without sacrificing integrity.
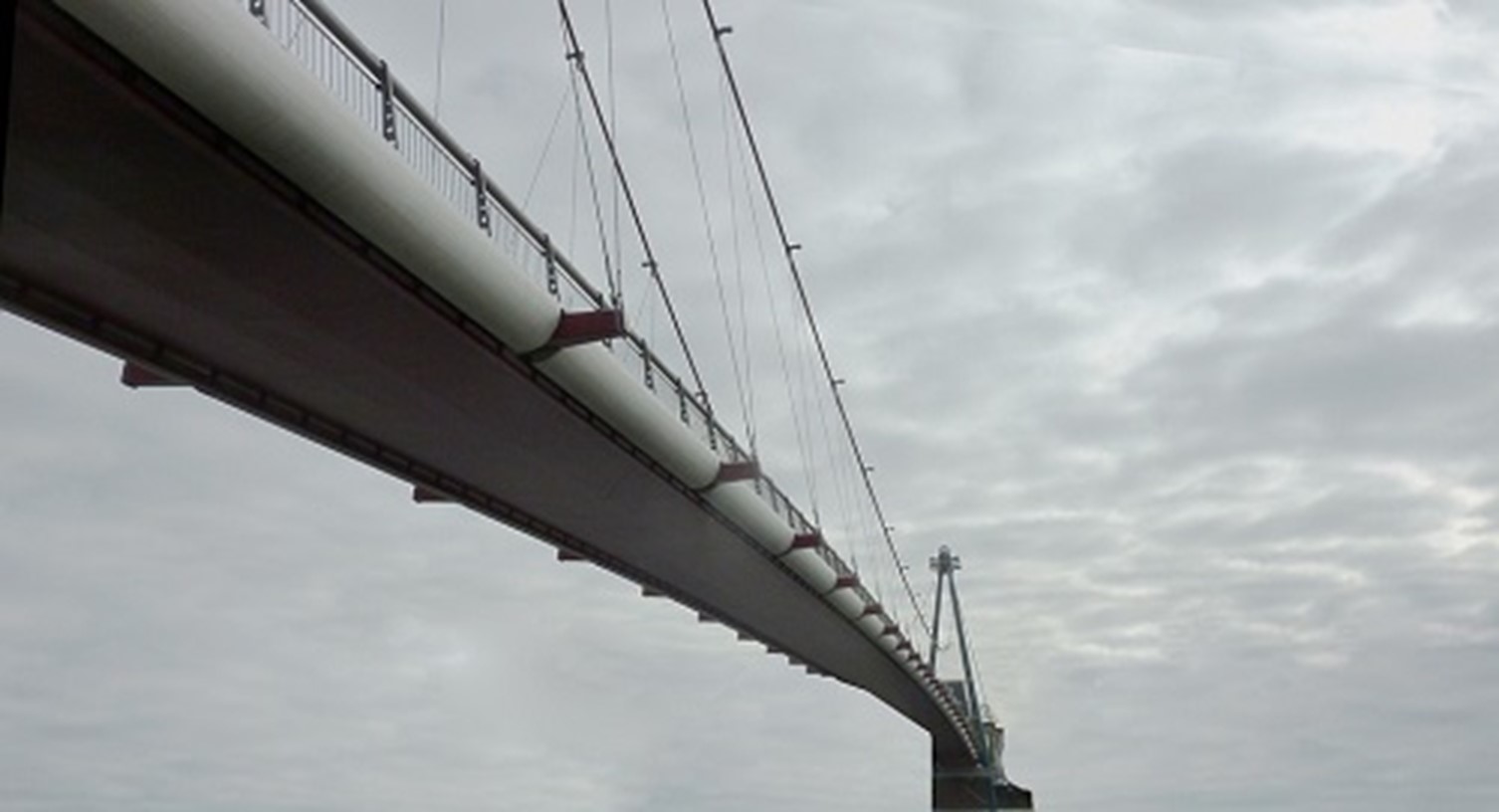
One of cold rolled steel’s most desirable aspects is its aesthetics. The cold rolling process enables metal processors like National Material Company to improve the surface finish. It leaves a smooth surface with few imperfections that are ideal if a project requires visual appeal. An excellent surface is great not just for its beauty, however. Cold rolled steel is used in the construction of bridges due to fewer visible surface flaws.
Additionally, cold rolled steel is ideal for projects that require more precision and need to be durable. Bars created with this technique have well-refined edges, and tubes are very straight with excellent concentric uniformity.
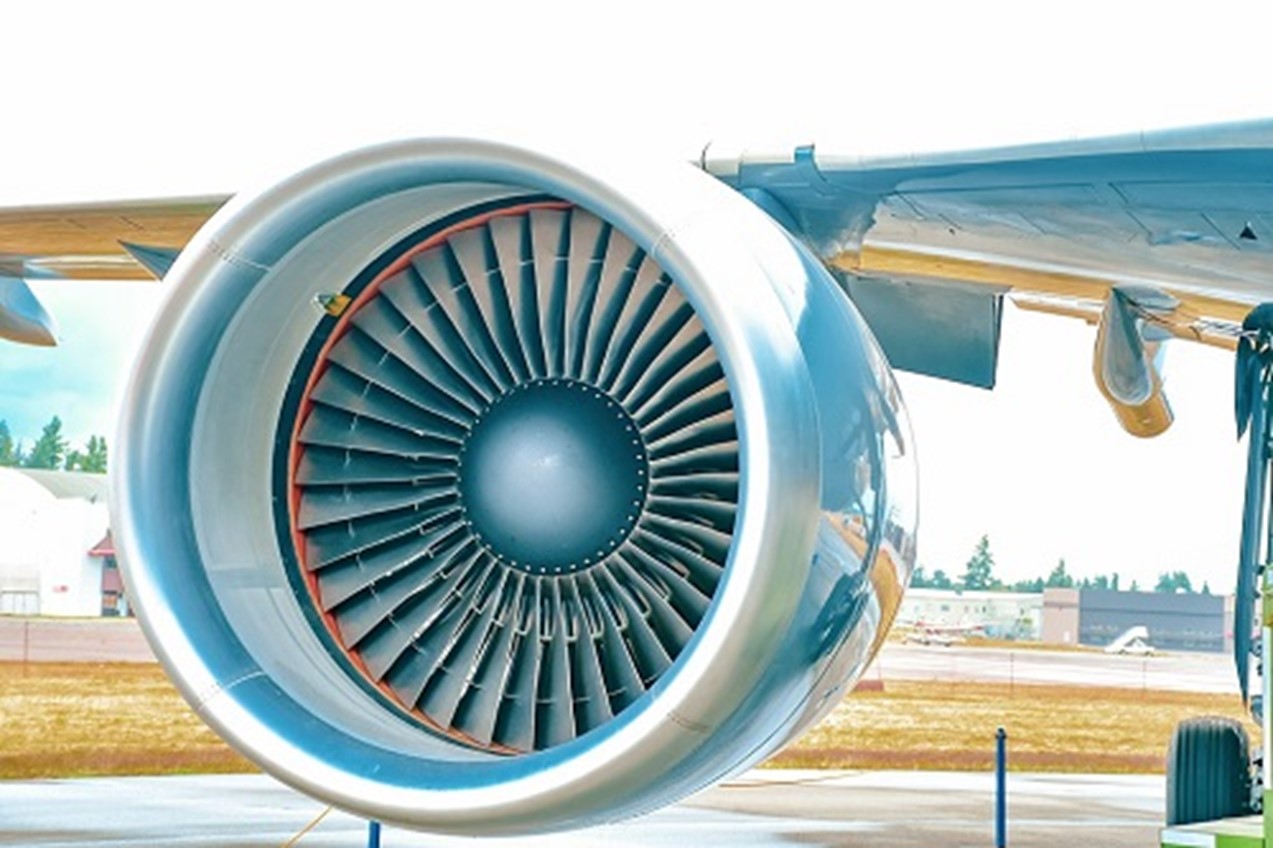
Cold rolled steel can be found across many industries today. It is used in parts for home appliances, roof and wall systems, metal furniture, aerospace structural members, and a wide scope of applications too numerous to list. Despite the many steps within the cold rolling process, cold rolled steel has a short manufacturing time and can be delivered promptly so customers can begin work on their projects quickly.
National Material Company continues to provide the most efficient and consistent delivery of a high quality product within the steel and metals processing industry. We are proud to be leaders in American steel service and look forward to leaving a legacy of excellence.
About Parent Company: National Material L.P.
Since its founding in 1964, National Material Limited Partnership (NMLP) has grown to over 30 business units and is now one of the largest metals processors in North America. Proud to be ISO-9002 certified and uncompromising in its safety standards for their employees, National Material is a company that leads the way through efficiency, innovation, and performance.
To find out more information about NMC’s products and services, please visit us at www.nationalmaterial.com or call (U.S.) 847-806-7200 to speak with a sales representative.