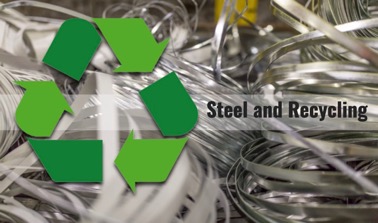
Here at National Material Company, we thought we’d pause, reflect, and share some good news and fun, interesting facts about the steel industry.
In 2016, Azo CleanTech reported that steel is the most recycled material in North America. The metal comes not only from cans but also from construction scraps, automobiles, and appliances, and it can be turned right back into steel that can be used in the same applications.
Recycling is at the core of the steel industry’s commitment to sustainability. According to steel.org, the North American steel-making furnaces “consume nearly 70 million tons of domestic steel scrap in the production of new steel.” By using steel scrap to make new steel, the North American steel industry conserves energy, emissions, raw materials, and natural resources. This commitment drives the reduction of steel’s environmental footprint, while producing advanced, highly-recycled steel products that meet an advancing society’s needs.
Here are some fun facts about steel and recycling:
- Steel products can be recycled repeatedly without loss of strength.
- Recycling steel saves the equivalent energy to power about 18 million households for a year.
- More than 80 million tons of steel are recycled each year in North America.
- For every ton of steel recycled, 2,500 pounds of iron ore, 1,400 pounds of coal, and 120 pounds of limestone are conserved.
- Almost 69 percent of all steel is recycled in North America each year – more than paper, aluminum, plastic, & glass combined. North America’s average steel recycling rate has been in excess of 60 percent since 1970.
- More than 95 percent of the water used for making steel in North America is recycled.
- One scrapped car produces more than four steel utility poles.
- 95 percent of the steel taken from commercial construction demolition sites was recycled and made into new steel products in 2002.
- 100 percent of a steel roof can be recycled. Asphalt roofs – zero percent. (Steel roofs provide your family with excellent protection against wind, water, snow, ice, and fire and are even hail-resistant. Asphalt roofs actually weigh twice as much as steel roofs. Steel roofs can last over 50 years, while traditional roofs last only 17 years!
- Steel food cans are the most recycled food package. 24,000 community recycling programs in North America collect steel cans. Canned food is as nutritious as its fresh and frozen counterparts upon preparation! Canned goods do not contain preservatives!!
- All 99 pounds of steel in the average major appliance can be recycled to make
new steel products.
Also, according to Utah Recycles, there are many more encouraging examples of how the steel industry’s commitment to recycling is helping to save the planet. Steel only takes up to 100 years to fully decompose in a landfill, whereas it takes plastic 1000 years to break down (aluminum can take 200 years, tin can take decades)! Recycling steel takes 25% less energy and creates only 25% of the water and air pollution required to produce steel from raw materials. About 70% of all metal is used just once, then discarded. The United States throws away enough iron and steel to continuously supply all of the nation’s automakers. Tin cans are made up mostly of steel, containing only about 0.15% tin and are 100% recyclable. 630 steel cans are recycled every second in the U.S. Recycling aluminum uses 90 percent less energy than making primary-production (virgin) aluminum! This is likely the reason that almost half of North American’s aluminum supply comes from secondary production (recycled aluminum).
Additionally, scrap metal recycling is an important and essential part of the manufacturing industry. According to the Institute of Scrap Industries, Inc, the scrap recycling industry in the United States transformed more than 130 million metric tons of materials into raw material commodities in 2015. More than half of this was steel, iron, and nonferrous metals like aluminum, copper, and lead. Using these secondary materials instead of virgin materials saves energy and reduces greenhouse gas emissions.
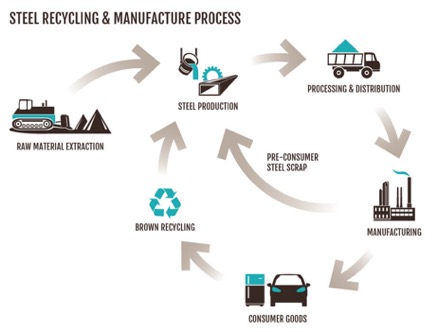
How is steel recycled?
The seven stages of steel recycling are collecting, separating, compacting, shredding, heating, refining, and solidifying.
1. Collecting
The first step in the steel-recycling process is the collection of scrap metal. End users such as construction or industrial workers place scrap metal in designated bins ready for pickup by a contracted recycling plant. Sometimes, the metal owner may need to transport the scrap metal to the contractor’s yard in preparation for recycling.
2. Separating
The next step involves using specialized magnetic equipment to separate recyclable items from the non-recyclable ones in the incoming scrap stream. Sorting is essentially the quality-control phase in the recycling process. This process is particularly important because the type of metal that is recycled affects the quality of the end product.
While steel is wholly recyclable, some steel items might contain non-recyclable content or parts that might lower the quality of the finished product. Sorting allows recyclers to produce high-quality steel that can stand up to the challenges present in industrial settings.
3. Compacting
After identifying the recyclable steel items, the recycling process officially begins as specialized machines crash and break the metal. This process minimizes the volume of the batch of scrap metal and makes the recycling process more efficient.
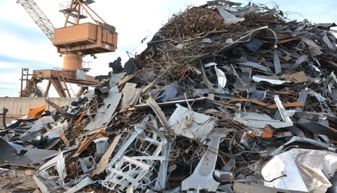
4. Shredding
After compacting the metal into manageable batches, the next step is breaking scrap into smaller pieces. Smaller metal pieces not only occupy less space but also require less energy to process, which can minimize carbon dioxide emissions.
5. Heating
Heating, or smelting, involves burning the shreds of steel metal over a large fire. For quality control purposes, recycling plants usually place different varieties of steel in separate furnaces. This process converts solid pieces of steel into liquid steel.
The amount of heat in each furnace depends on the alloying elements present in the scrap steel. Depending on the intensity of the heat and the amount of metal one is burning, the smelting process can take a few minutes or several hours.
6. Refining
Refining eliminates dirt, debris, particles, and other impurities that may be present in the melted steel. Steel recycling plants use various methods to purify smelted steel. Common techniques include electrolysis, distillation, zone refining, and chromatography.
Each purification method has its own advantages and disadvantages, and the quality of the end product varies from one refining technique to another.
7. Solidifying
In this next step, the pure melted steel is ready for cooling and solidification. Recycling plants use advanced systems to transfer hot molten metal from the heating and purification chambers to the cooling containers.
Additional chemical compounds help to stabilize the molten steel and ensure that the final product retains its desired properties, including weight, density, heat conductivity, and corrosion resistance.
Recyclers use specialty containers to shape molten steel into structural steel, which comes in different shapes and sizes for use across multiple industries. Examples of structural steel include bar stock, I-beams, pipes, tees, angled stock, hollow steel sections, and American standard beams.
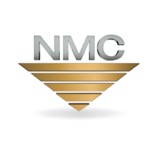
The National Material Company Commitment
By virtue of being a prominent leader in the steel industry, National Material Company (NMC) has made a commitment to reducing their carbon footprint. We rely on efficient production methods and testing to ensure that we are always in line with energy reduction standards.
NMC has made many commitments, in fact. We are committed to ensuring that a wide number of industries receive the best steel product possible.
Some industries we serve:
- Automotive
- Agricultural
- Appliance
- Office furniture
- Computer
- Construction
- Military
- Heavy truck
- Consumer products
- High pressure vessels
- Generator manufacturing
- Industrial equipment
Services offered:
- Galvanized Steel
- Advanced high–strength steel (AHSS)
- Steel slitting
- Blanking
- Pickling
- Cut-to-length processing
Visit our website for more details about our capabilities and our case studies.
About NMC
NMC is proud to offer high quality galvanized steel and galvanized Advanced High-Strength Steel. The treatment with zinc offers a long-lasting corrosion and rust-resistant alloy. NMC continues to further increase our leadership position in the domestic and international steel industry by providing high quality products ensuring the success of your next project.
About Parent Company National Material L.P. – With more than 3,000 employees from a multinational portfolio of companies, NMLP provides engineered metal products, which include aluminum extrusion and stainless steel rolled product companies, to automotive, aerospace, construction, defense, electrical, and industrial markets.
Become a customer today! Visit NMC at https://www.nationalmaterial.com/. Or you can contact sales via our website or call us at 847-806-7200.