The process of steel blanking has become prominent in the steel manufacturing industry because of its ability to make highly specialized parts that minimize waste and cost. With steel blanking, the goal is to use what is stamped/punched out rather than what is left after going through the die. Simply, the punched-out piece IS the part. Let’s look at how this process works, how it differs from other processes, and its overall benefits.
What is steel blanking?
Blanking is a steel manufacturing process in which a flat, geometric shape (or “blank”) is created by feeding a coil of sheet metal into a press and die. In this process the blank is punched out from large metal sheet. Here is visual depiction of this process:
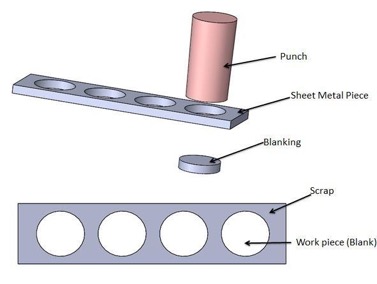
Press Blanking machinery can typically process material up to 72 inches (1828mm) wide and .250 inches (6.35mm) thick from coils up to 80,000 lbs. Typically multiple sheets are blanked in a single operation and the blanked parts will require secondary finishing to smooth out burrs along the bottom edge.
How does steel blanking differ from other process?
Other, similarly natured processes include punching and piercing. Both remove material from a metal sheet but the end results differ from steel blanking.
Punching is also a material removal process but rather than the final product being the punched out material, like in blanking, metal is removed so that the sheet metal itself is the final product. An easy way to differentiate is to think of a piece of paper that you punch a hole through. Blanking uses the circular piece as the final product while punching uses the piece of paper with the hole in it as the final product.
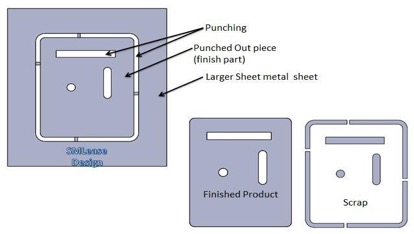
Another similar process is piercing, in which a punch operation cuts a hole by tearing operation from a final piece of sheet metal. This is process is considered a blanking operation.
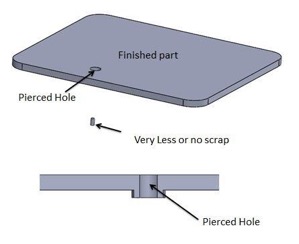
Steel Blanking Advantages
Steel blanking produces economical metal pieces that are customized to fit specific customer needs. In the blanking process the material is continually fed into the machine which leads toless setup and parts management. Simply, steel blanking allows you to make more with less.
This reduces waste significantly because the tools are typically designed to nest parts as close together as possible. Also, shipping costs are reduced by only sending the net weight and leaving the rest behind.
Industries that use steel blanking
Commonly, a press blanking line is designed to meet the high-quality demands of the automotive and fabricating industries. This includes suppliers of “surface exposed” panels and other auxiliary sectors. The industries that use blanking material will likely expand. This is due to the ability for blanks to adapt to the final shape of the part which appeals to a wide variety of industrial industries.
NMC’s Steel Blanking Capabilities
National Material is a steel service center that delivers comprehensive blanking consultation (see NMC’s blanking capabilities) (insert link: https://www.nationalmaterial.com/steel-processing-capabilities/blanking/) with designs beyond being “just a place that makes the part.” An essential part of quality blanking production is not only listening to a request but adding value. We work to minimize waste, accelerate parts per moment, and deliver a part that exceeds standards. The proof is in the numbers; here are some of the technical benefits of blanking:
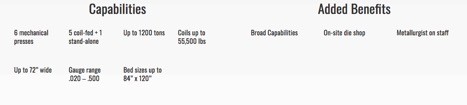
If you believe your company can benefit from our blanking services, please visit us at https://www.nationalmaterial.com or call (U.S.) 847-806-7200 to discuss how we can be of service.
About National Material L.P. – Since its founding in 1964, National Material Limited Partnership has grown to over 30 business units and is now one of the largest suppliers of steel in America. The National Material group of industrial businesses consists of the Steel Group, Stainless and Alloys Group, Raw Material Trading Group, Aluminum Group, and Related Operations.