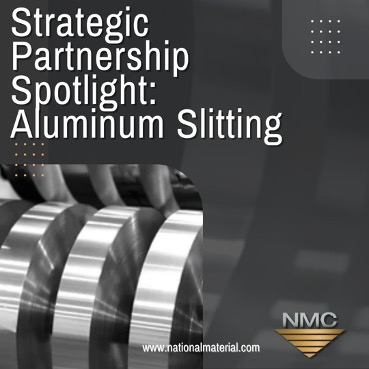
So, what exactly can one expect from NMC’s aluminum slitting services? Envision a full symphony, where every instrument — from the delicate violin to the mighty timpani — harmoniously combines efforts under the baton of a capable conductor, and the result is a beautiful, well-constructed piece of music.
Aluminum Slitting — like a full symphony — represents a manufacturing process where machinery and tools cut aluminum or steel into various widths. In a nutshell, a slitting line performs this operation, commencing when an uncoiler machine feeds and uncoils coiled aluminum or steel sheets. Subsequently, the material passes through the slitter head, which cuts it into long strips (mults) according to specifications. Rigorous tests and quality checks then verify the precision-cut mults before recoiling, packing, and shipping them to various industries worldwide.
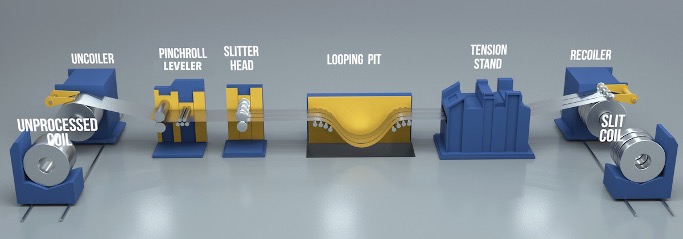
The Aluminum Slitting Line and Its Components
The entire slitting operation, particularly the slitting line, executes a straightforward steel and aluminum slitting process. For example, like a bicycle chain set, each link plays a key role in ensuring precise flow and the production of quality end products. Let’s explore these key elements:
Uncoiler:
Initially loading the large steel or aluminum coil, the uncoiler unwinds the coil as it feeds the metal strip into the slitting section. It operates a tension control system to maintain proper strip tension during the process.
Entry Guide:
A cylindrical device at the entrance of a tube mill maintains the strip on the mill centerline so that the forming process uniformly bends the material.
Slitter Head:
The slitter head, the heart of the slitting machine, consists of a set of rotary knives or blades that precisely cut along the length of the metal strip. Operators adjust these blades to achieve the desired strip width.
Loop Pit or Pit Table:
A controlled area for the metal strip to form a loop, the loop pit or pit table helps maintain consistent tension during the slitting process and prevents damage to the strip.
Tension Control System:
Essential for maintaining proper tension throughout the process, tension control systems adjust the speed at which the metal strip is fed to prevent issues like wrinkling or stretching.
Recoilers:
After the slitting process, the narrower strips wind onto recoiler mandrels. Multiple recoilers may process different widths simultaneously. They feature tension control mechanisms to ensure uniform winding.
Recoiler Mandrels:
Spindles onto which the slit strips wind, recoiler mandrels are designed to accommodate various coil sizes. They include features like expandable segments to secure the strips.
Control Panel:
Modern slitting machines feature computerized control panels allowing operators to set and monitor various parameters, such as strip width, tension, and blade position.
Safety Features:
Safety in metal slitting operations is paramount. Emergency stop buttons, guards, and sensors detect potential hazards.
Material Handling Equipment:
Lastly, cranes, coil cars, and forklifts load and unload large coils and transport slit strips and coils within the facility.
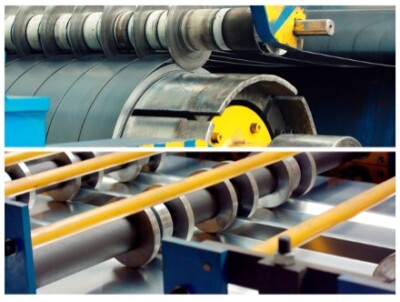
Different Types of Slitting
A typical slitting line is comprised of three essential components: an uncoiler, a slitter, and a recoiler, all of which have separate motors. The specific mode that drives the aluminum or steel master coil through the slitter knives is determined by several factors, including the material type, sheet thickness, and the required number of slits.
Straight Mode Slitting:
The recoiler pulls the master coil from the uncoiler through the slitters. When both the uncoiler and slitter actively drive the material toward the recoiler, this method is known as “pull-through slitting.”
Driven Slitting:
The slitter itself is also actively driven during the process. This involves synchronizing motors to maintain a constant speed as the material advances along the processing line. Driven slitting excels in its capability to effectively handle thinner sheets and deliver superior edge quality across various material thicknesses.
Free Loop Slitting:
A pit is integrated into the line. This pit serves to accommodate the processed coil strips, aiding in the absorption of any length differential within the slit coils. Typically, the slitter is responsible for powering both the uncoiling and slitting of the material, while the recoiler takes charge of rewinding the material.
Overall, slitting is a cost-effective, sustainable, and efficient method of processing aluminum and steel coil sheets to a wide range of narrow widths for all your needs. In fact, slit coils find use in most industries: automotive, agricultural, and construction, military, and aerospace applications.
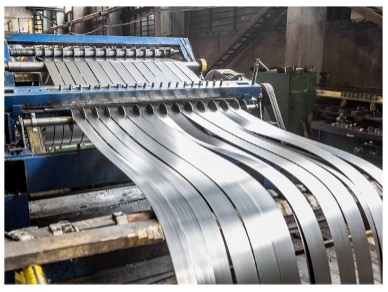
As one of the industry’s top steel and aluminum suppliers and processors, National Material Company leverages precision aluminum and steel coil slitting capabilities through our strategic partnerships and years of experience and innovation. With that said, the diverse supply chain can cater to all your slitting specifications.
NMC’s aluminum and steel slitting services offer:
- 1-72” min. / max. slit width
- 74,000 lbs. max. weight
- Reduced turnaround time
- Reduced scrap
- Reduced costs
- Precise cut according to your specifications
- Streamlined material flow
- Ease of doing business
- ISO-9002 certified
NMC is part of the National Material Limited Partnership (NMLP) steel division — one of the largest independent steel service centers in the United States. NMLP operates 16 steel service centers and processing facilities in the United States, Canada, and Mexico that ship over 2,000,000 tons of steel annually. As a matter of fact, NMC runs ten of these steel processing facilities and service centers located in the U.S. and Mexico. These locations are a key advantage for our customers in terms of logistics and cost.
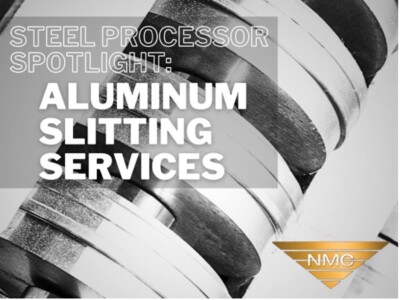
About National Material L.P.
Since its founding in 1964, the National Material Limited Partnership has grown to over 30 business units and is now one of the largest suppliers of steel in North America. The National Material group of industrial businesses consists of the Steel Group, Stainless and Alloys Group, Raw Material Trading Group, Aluminum Group, and Related Operations.
Please view our capabilities at nationalmaterial.com/company or call (U.S.) 847-806-7200 to discuss how we can be of service.